Contact Us
Tel: 0086 755 23248547
Fax: 0086 755 23248547
Skype:simon9969@hotmail.com
Linkman:Simon Gao
Postcode:518106
Web: www. injection-flow.com
E-mail:simon@mpa-tooling.com
Address: Building Yonghui, No. 202, Changchun north Road, Guangming new district, Shenzhen city, China
Cooling Analysis
Mold Cooling Simulation to Reduce Cycle Times
Reduce Cycle Times by 20%. ( See stats below )
Mould Cooling simulation allow MPA to optimize mold and cooling circuit design to achieve uniform part cooling, minimize cycle times, minimise part warpage due to cooling factors, and decrease overall manufacturing costs. ie Increase Profit.
Mould Cooling simulation allow MPA to optimize mold and cooling circuit design to achieve uniform part cooling, minimize cycle times, minimise part warpage due to cooling factors, and decrease overall manufacturing costs. ie Increase Profit.
Cooling Channel Design & Optimization
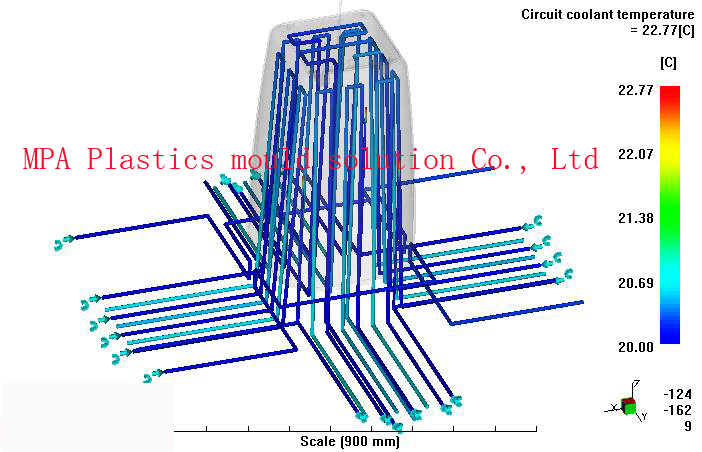
Typical savings in the order of 20% on cycle time are not uncommon while also using less cooling water and maintaining more even cavity surface temperature profiles.
A number of well placed cooling channels may have slight increase on the tool manufacture cost, but the payback via a shorter cycle time will result in a phenomenal increase in life time profit.
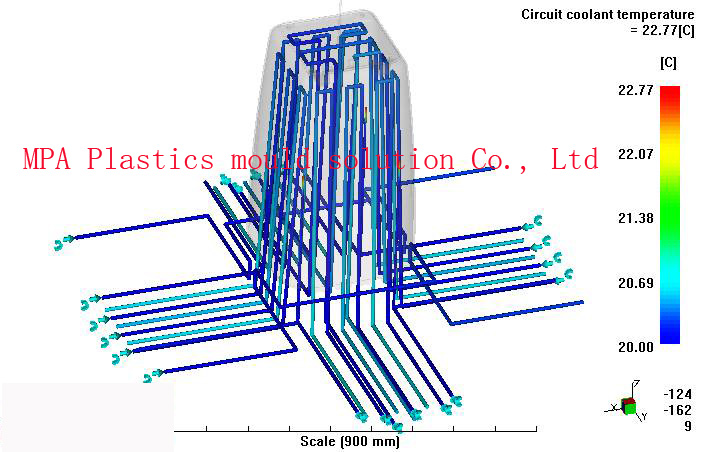
A recent study conducted on a thick wall PP moulding helped reduce the cycle time from 215 seconds to 120 seconds with out any compromise on surface finish. The savings were achieved by adding several baffles/fountains to deep pockets and incorporating high conductivity inserts. Contact us and ask about cycle time reduction. Just a couple of seconds reduction in cycle time can save thousands of dollars in machine time over the product life cycle.
Mold Surface Temperature

Cooling Analysis Capability:
Optimize part and mold designs to achieve uniform cooling with the minimum cycle time
View the temperature difference between the core and cavity mold surfaces
Minimize unbalanced cooling and residual stress to reduce or eliminate part warpage
Predict temperature for all surfaces within the mold: part, runners, cooling channels, inserts
Predict the required cooling time for the part and cold runner to determine overall cycle time
View the temperature difference between the core and cavity mold surfaces
Minimize unbalanced cooling and residual stress to reduce or eliminate part warpage
Predict temperature for all surfaces within the mold: part, runners, cooling channels, inserts
Predict the required cooling time for the part and cold runner to determine overall cycle time
2005-2015 © Copyright MPA Mold flow analysis Tel:0086 755 23248547 Fax:0086 755 23248547
Sales Representative:simon@mpa-tooling.com